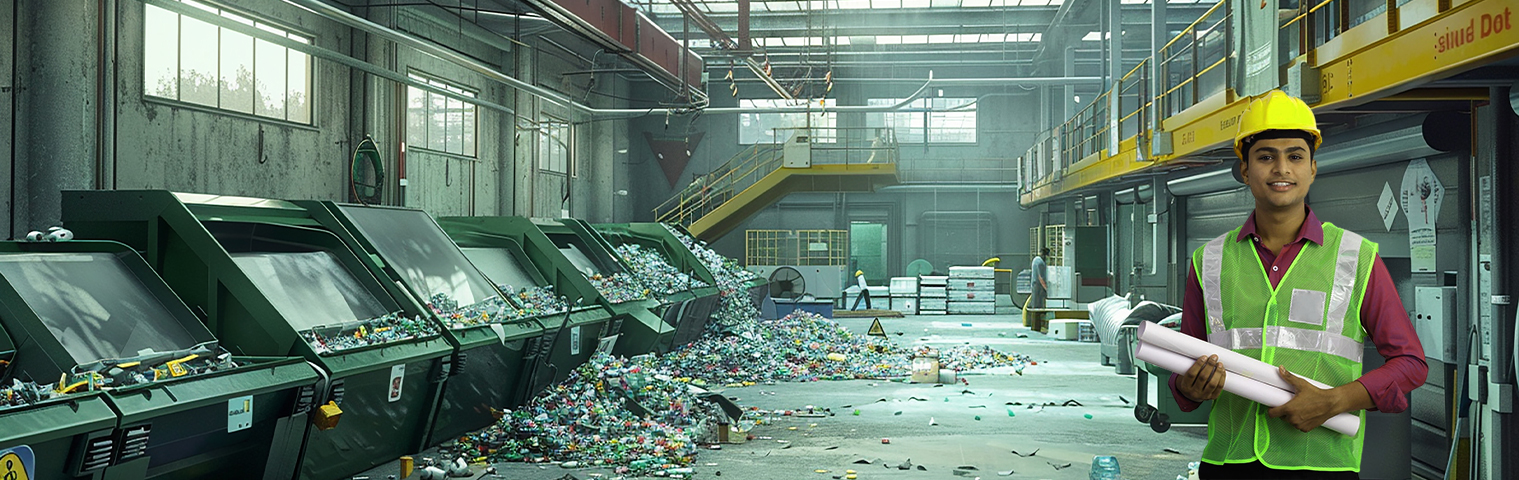
An Engineer’s perspective on Plastics: Beyond Buckets and Mugs
When most people think of plastics, they envision everyday items like mugs, buckets, and packaging. However, the world of plastics extends far beyond these common uses. Plastics are integral to many advanced applications, driving innovation and efficiency in various industries. Let’s explore how different types of plastics are revolutionizing advanced fields such as energy generation, aerospace, marine, defense, medical, and automotive industries.
The earliest known use of plastic dates back to the Mayan civilization, with evidence suggesting that they created a plastic-like material around 1000-1600 CE. This material, known as “Maya gum,” was derived from the sap of the sapodilla tree (Manilkara Zapota) and was used for various purposes, including crafting jewelry, tools, and decorative items. It is believed that the Mayans achieved this through a process of boiling the sap with lime and then mixing it with other natural materials. The first man made plastic, Parkensine was invented by Alexender Parkes in 1862, plastics have come a long way. The first mass producible polymer was made late in the first decade of 20th century where Leo Baekeland synthesized the first fully synthetic polymer, Bakelite which could be mass manufactured. Initially developed as a substitute for natural materials like ivory, shellac, amber and tortoiseshell, plastics quickly found applications in consumer goods. Over time, advances in polymer chemistry have expanded the properties and uses of plastics, making them essential in modern technology and industry for advanced applications such as:
- Solar Panels: One of the key materials in solar panel construction is Polyvinyl Fluoride (PVF), used in the backsheets of photovoltaic modules. PVF provides excellent weather resistance, protecting the panels from environmental degradation. Ethylene-Vinyl Acetate (EVA) is another crucial plastic, used as an encapsulant to cushion and protect the delicate solar cells within the panels. Polydimethylsiloxane is used as a protective layer, and Polymethyl Methacrylate is used in solar concentrators and light guides.
- Wind Turbines: The blades of wind turbines are often made from Epoxy Resins and Polyester Resins. These materials offer a combination of high strength, light weight, and resistance to environmental factors, making them ideal for withstanding the mechanical stresses and harsh conditions experienced by wind turbines. Glass Fiber Reinforced Polymers are used for turbine blades, and Polyurethane (PU) for blade coatings.
- Aerospace: The aerospace industry demands materials that offer high performance under extreme conditions. Polyether Ether Ketone (PEEK) is a high-performance thermoplastic that excels in such environments. PEEK is known for its exceptional mechanical properties, chemical resistance, and ability to withstand high temperatures. It is used in various aerospace components, including bearings, seals, and insulators. Carbon Fiber Reinforced Polymers (CFRP) are another critical material in aerospace. These composites, made from carbon fibers and an epoxy resin matrix, provide an excellent strength-to-weight ratio. This property is essential for aircraft structures, as reducing weight improves fuel efficiency and reduces emissions. The Boeing 787 Dreamliner, for example, utilizes CFRP for 50% of its primary structure, including the fuselage and wings. Polyimide (PI) is used in insulation films and adhesives, and Polytetrafluoroethylene (PTFE) in seals and gaskets.
- Marine Applications: Marine environments are harsh and demanding, requiring materials that can withstand saltwater, UV radiation, and mechanical stress. Polyethylene (PE) and Polypropylene (PP) are commonly used in marine applications due to their resistance to water, chemicals, and UV light. These plastics are found in ropes, nets, and various marine equipment. PU is another important plastic in marine applications, often used in coatings and sealants to protect vessels from corrosion. PU’s durability and flexibility make it ideal for use in harsh marine conditions, ensuring the longevity and safety of marine structures and equipment. Polyvinyl Chloride (PVC) is used in piping, fittings, and coatings, and Nylon in ropes, nets, and marine equipment.
- Defense: In the defense industry, materials must provide exceptional protection while being lightweight and durable. Aramid Fibers, such as Kevlar, are used in bulletproof vests and helmets due to their high strength-to-weight ratio and resistance to impact. These materials provide critical protection for military personnel in combat situations. Polycarbonate (PC) is another vital plastic in defense applications. Known for its impact resistance, PC is used in visors, protective goggles, and aircraft windows. Its ability to withstand high impacts while remaining lightweight makes it an ideal material for protective gear and equipment. Ultra-High-Molecular-Weight Polyethylene (UHMWPE) is used in body armor and ballistic protection, and Epoxy Resins in composite armor systems.
- Medical Applications: The medical field relies heavily on plastics for a wide range of applications due to their biocompatibility, sterility, and versatility. PE and PP are commonly used in medical devices such as syringes, tubing, and containers. These plastics are safe for use in medical environments and can be easily sterilized. Polylactic Acid (PLA) is a biodegradable plastic used in medical implants and sutures. PLA’s ability to safely degrade within the body makes it ideal for temporary medical applications, reducing the need for additional surgeries to remove implants or sutures. PC is used in medical devices and syringes, and Thermoplastic Polyurethane in medical tubing and catheters.
- Automotive Industry: The automotive industry benefits from plastics in numerous ways, from improving fuel efficiency to enhancing safety and comfort. Acrylonitrile Butadiene Styrene (ABS) is used in dashboard components, trims, and other interior parts due to its durability and ease of molding. ABS’s versatility allows for the creation of complex shapes and designs, contributing to the functionality and aesthetics of vehicle interiors. PU is used in seats, insulation, and foam padding for its comfort and energy absorption properties. PU’s ability to provide cushioning and support makes it essential for enhancing passenger comfort and safety in vehicles. Nylon is used in under-the-hood components and fuel lines, and Polycarbonate-Acrylonitrile Butadiene Styrene in exterior parts like bumpers.
Plastics are far more than just the materials used for everyday items like mugs and buckets. They play a crucial role in advanced applications across various industries, driving innovation and improving performance. From renewable energy and aerospace to marine, defense, medical, and automotive applications, plastics are essential to modern technology and industry. By understanding the diverse uses of plastics, we can better appreciate their value and importance in our daily lives and beyond.
Interested in the topic? Get in touch to know more!
This blog is authored by Dr. Prashant Gupta, Sr. Asst. Professor, School of Engineering, Plastindia International University.
Similar Posts:
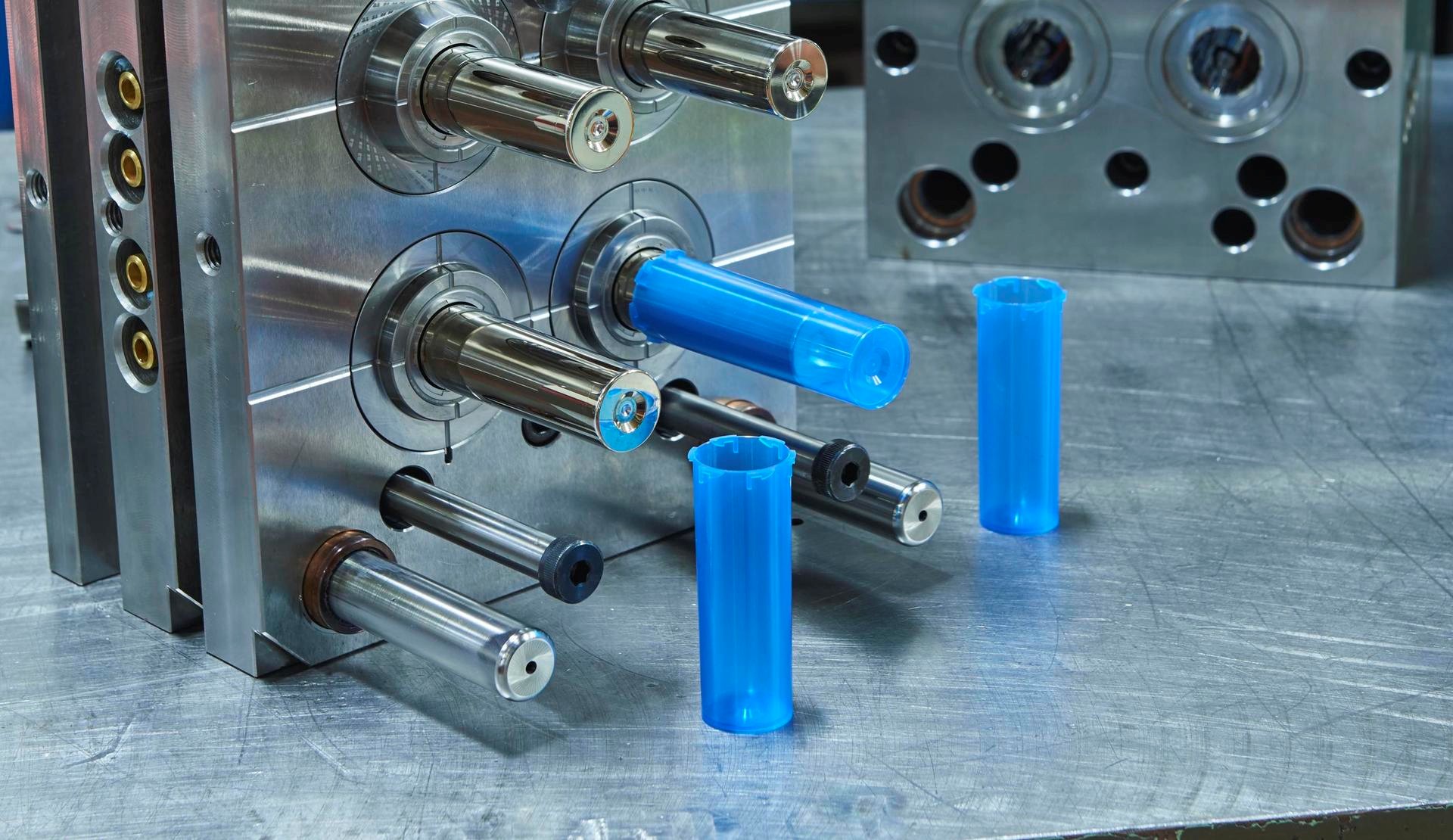
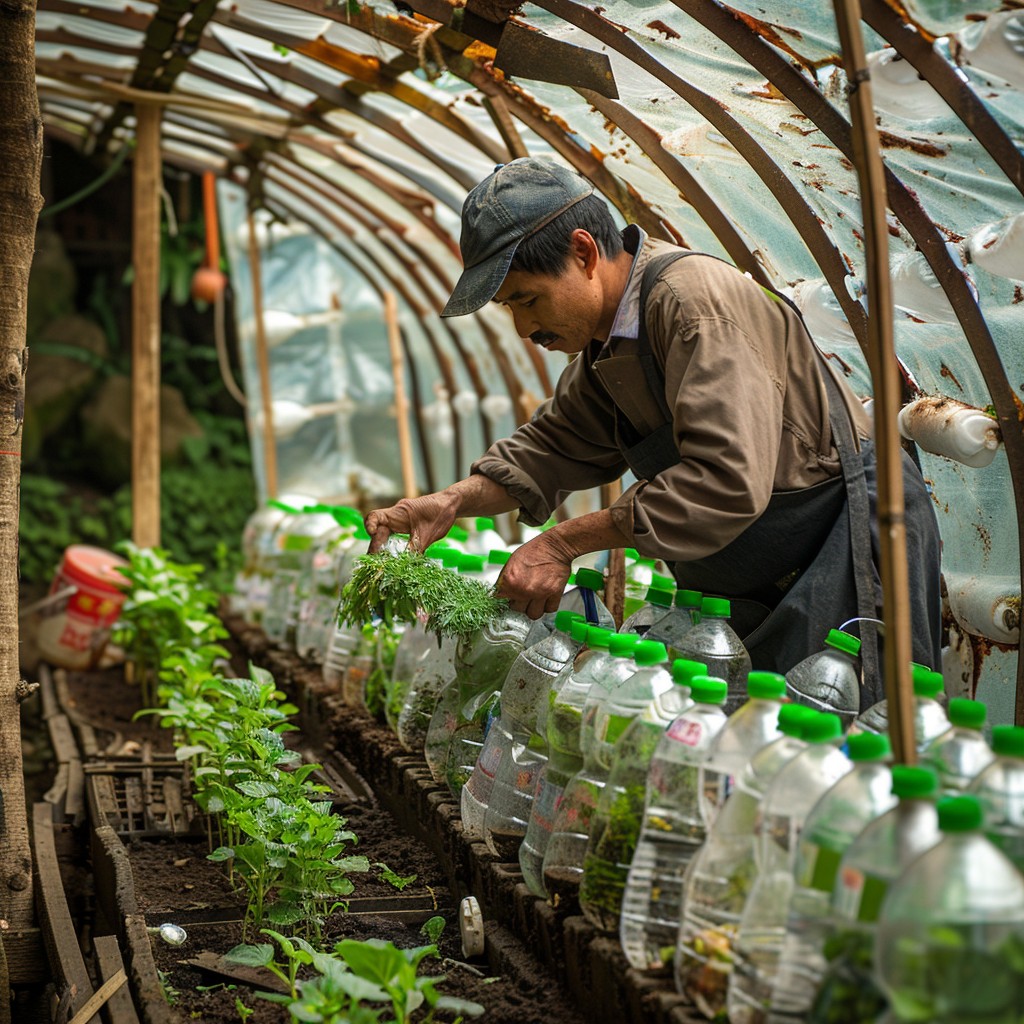
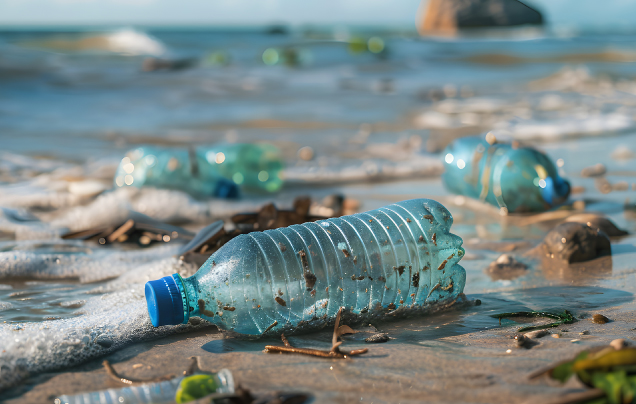